Subcontracting is a critical process for many organizations, and from an SD consultant’s perspective it’s quite unique. Let’s take a closer look at the handoff from Purchasing to the SD Delivery. Read on for more about the SAP Subcontracting PO Delivery Setup.
What is Subcontracting?
In general terms, subcontracting is the outsourcing of some process to an external vendor. Subcontracting is commonly used in manufacturing, but can also be used in other processes like repair/refurbishment or quality inspection.
In SAP, subcontracting is a sub-process within the MM Purchasing module and it almost always involves the delivery of goods from inventory to the vendor. To illustrate with an example, your company manufactures lenses. Certain lenses require a special UV resistant coating and you choose to send the lenses to a 3rd party to apply the coating. You create a delivery for the lenses to be shipped to your vendor. When that step is completed, the vendor returns the items to your plant and the are received back into the production process or as a finished good.
SAP Subcontracting Process Overview
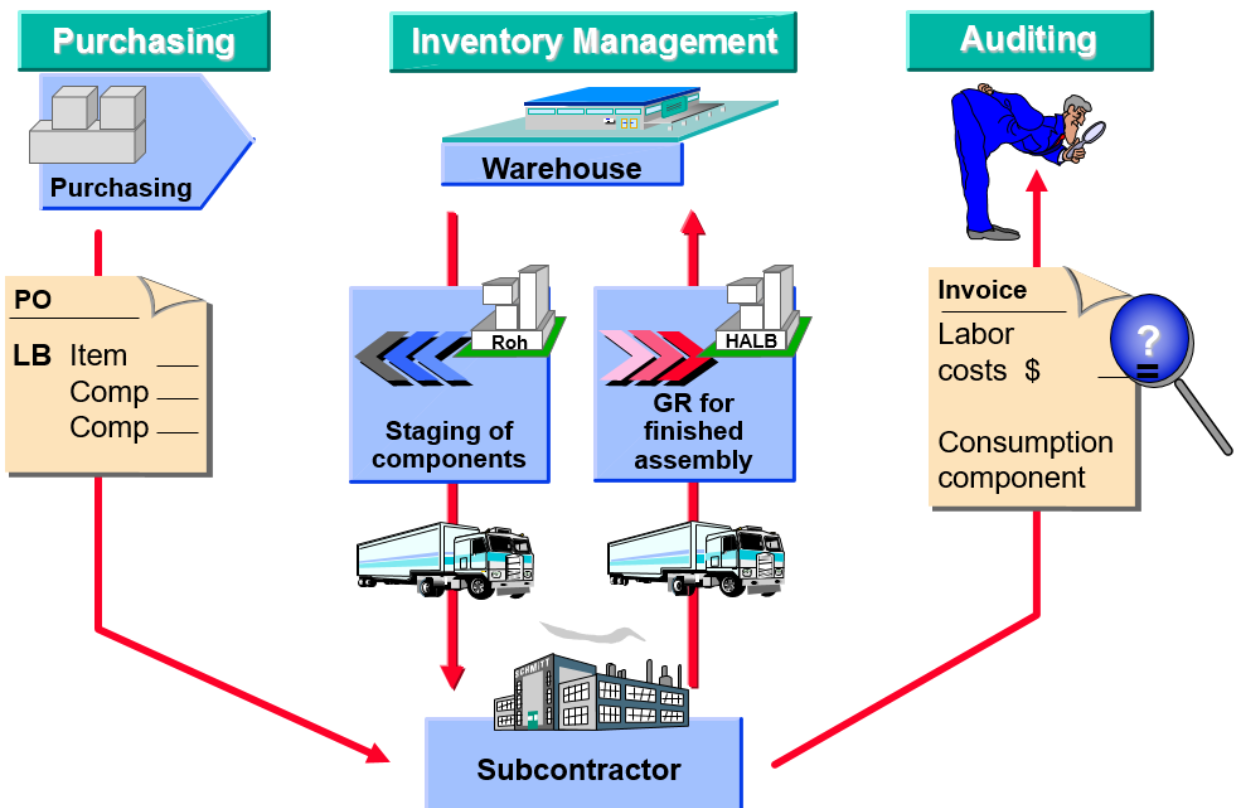
No matter which process is utilizing subcontracting, it will always involve a Purchase Order. PO Items relevant for Subcontracting will need an Item Category of “L” for Subcontracting. Adding this value will open up the “Components” button located on the item Material Data tab. This is where you maintain all the components which need to be sent to the vendor. This can be done either manually or through the use of a BOM.
Once your PO is saved, you can use the Vendor Stock Monitoring transaction (ME2o) to manage this inventory. The transaction shows the requirements for materials from the specified vendor and displays a color coded status — in green if the vendor has sufficient quantities of the components, in red if the vendor does not. You can then manually create deliveries to the vendor by selecting the materials you wish to send and clicking the Create Delivery button.
Subcontracting Delivery Configuration
There’s actually quite a bit that goes into the Subcontracting with delivery process. First, we’ll start with…
Prerequisites
It goes without saying that you’ll need some basic things setup before tackling the rest of this process:
- Relating to Enterprise Structure, you’ll need some basics:
- Your delivering plant must be setup. This is the plant specified on your PO as the originating plant for the components.
- A Sales Area must be setup and assignable to your Vendor/Customer.
- And, of course, your Master Data must be setup:
- Your vendor master must be setup in your Purchasing Org.
- A customer master must be setup in your Sales Area. A Ship-to should suffice (a.k.a. Goods Recipient). This customer master will be assigned to your vendor to enable the logistics process.
- A BOM is an optional piece of master data which can help pre-populate your Components information on the PO.
Let’s now get into some details…
Standard Configuration
This is the part that I found interesting. Generally, SAP SD processes rely upon copy controls to define how documents and data are copied from the source (i.e. Sales Order) to the destination (i.e. Delivery). However, there is no copy control from an Subcontracting PO to an SD Delivery. So, how does SAP know when and how to copy data between these two objects?
The process uses what you could call a ‘Dummy’ Sales Document Type. As mentioned previously, the Subcontracting delivery keys off of a Purchase Order. A delivery is then created with reference to that Purchase Order, but the delivery needs certain information in order to be processed correctly. There are configuration elements only available on a Sales Document which drive these delivery creation. Delivery Basics like logistics defaults, pricing for freight, and partner determination have to come from somewhere. A Dummy Sales Document type is used to allow things like Copy Controls to be used for this unique process.
I’m going to highlight the standard configuration as it exists within a standard S/4 HANA system. There are 4 key areas:
- Assignment of the Subcontracting Delivery Type (LB) to the Delivering Plant
- Assignment of the Default (Dummy) Sales Order Type (DL) to the Subcontracting Delivery Type
- Configuration of the Default Order Type Setup (DL)
- Assignment of Copy Control Settings between the Sales Order (DL) and the Delivery (LB)
1. Assignment of the Subcontracting Delivery Type (LB) to the Delivering Plant
The Subcontracting configuration starts with the assignment of a Delivery Type to the Delivering Plant for use in the Subcontracting process. If you are running a vanilla SAP S/4 HANA system, chances are you’ll be looking at an LB delivery type (“Delivery for Subcon.”). To access this piece of configuration, you’ll want to navigate to the IMG node below:
IMG → Materials Management → Purchasing → Purchase Order → Set Up Subcontract Order
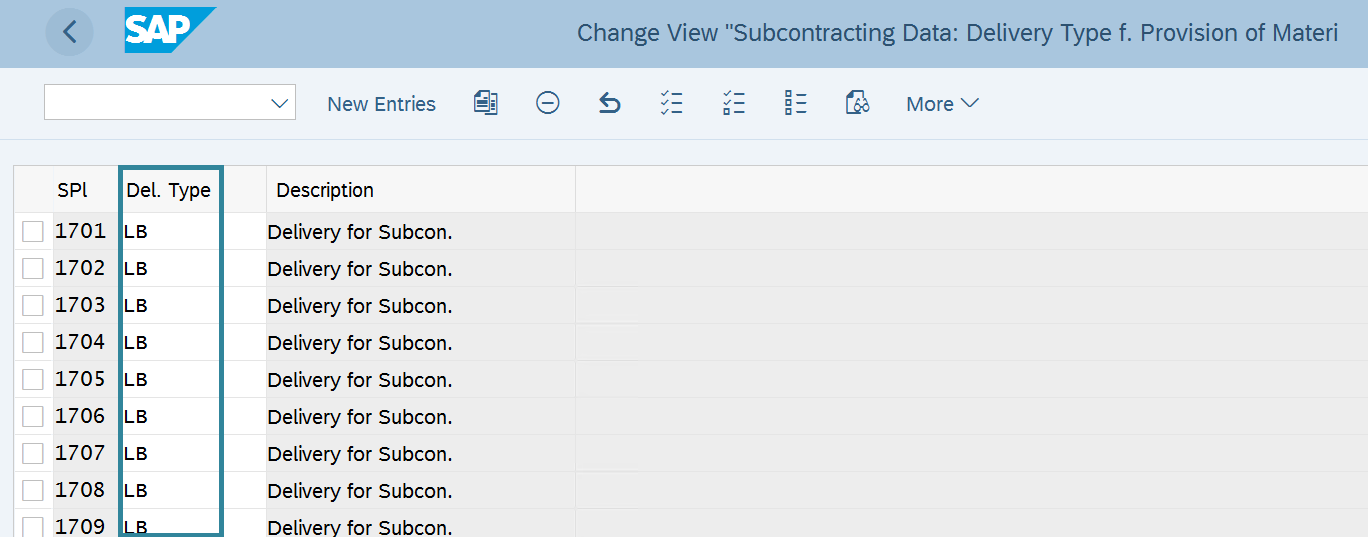
There’s not much more here than assigning the plant to the Delivery Type. It appears that you are limited to only one default Delivery Type per Plant.
2. Assignment of the Default (Dummy) Sales Order Type to the Subcontracting Delivery Type
If you take a look at the delivery type defined in step (1), you’ll notice a setting in the ‘Order Reference’ area called ‘Default ord.ty.’. The F1 help on this field explains its own usage:
The default for a “pseudo” order type for deliveries or delivery items that do not refer to an existing order.
Essentially, this order type is the stand-in for what would be a normal order type in a standard OTC scenario. Use the IMG path below for this piece of the config:
IMG → Logistics Execution → Shipping → Deliveries → Define Delivery Types
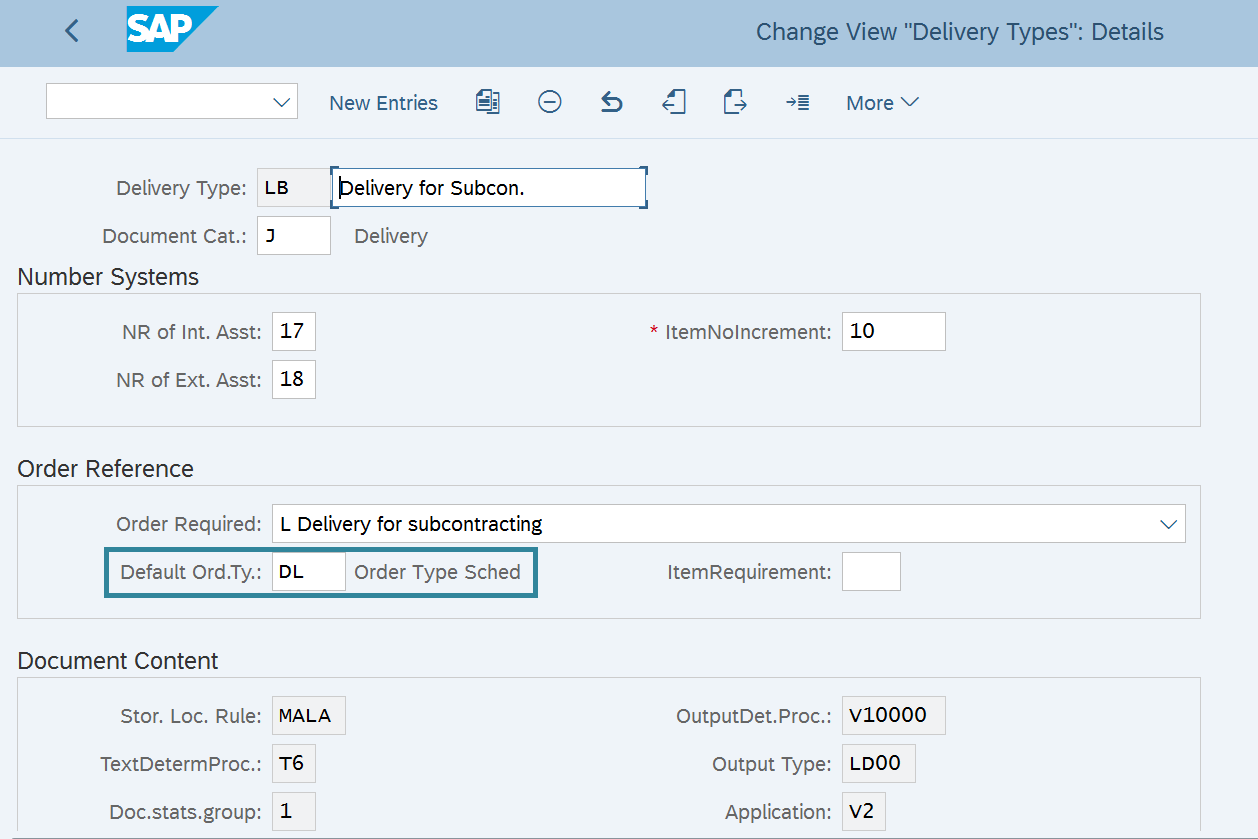
The only field worth mentioning is that ‘Default Order Type’ field; the rest of this is standard delivery setup.
3. Default Order Type Setup
I’m not sure if there’s actually much to look at in the setup of this Sales Document Type. There are relatively few logistics-related fields. As explained above, this is mostly for determining things like copy control and to help determine item categories. You probably know where this configuration is, but for the noobs:
IMG → Sales and Distribution → Sales Document Header → Define Sales Document Types
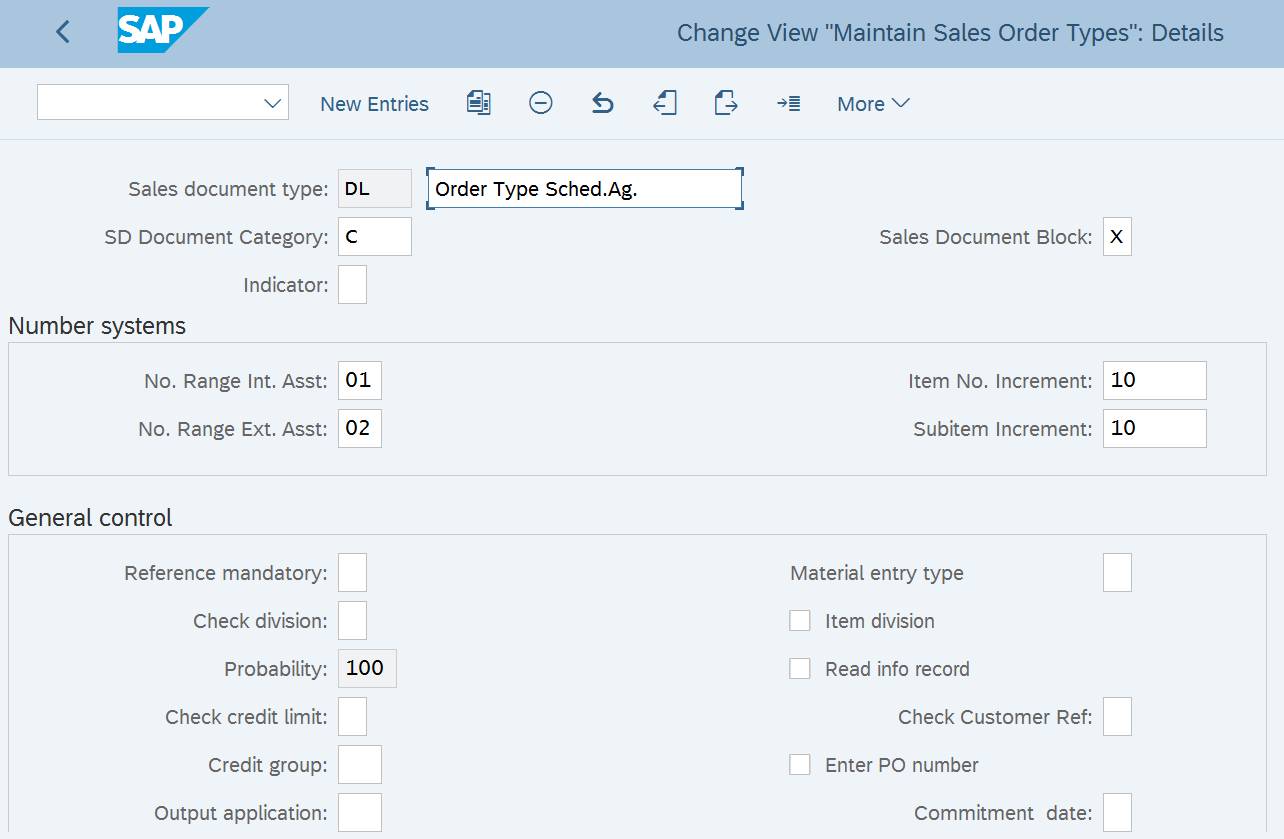
These are all default settings, so… again… not much to say here.
4. Setup Copy Control
The final step is the setup of the copy control between your dummy Sales Document type (DL) and your Subcontracting delivery type (LB).
Logistics Execution → Shipping → Copying Control → Specify Copy Control for Deliveries
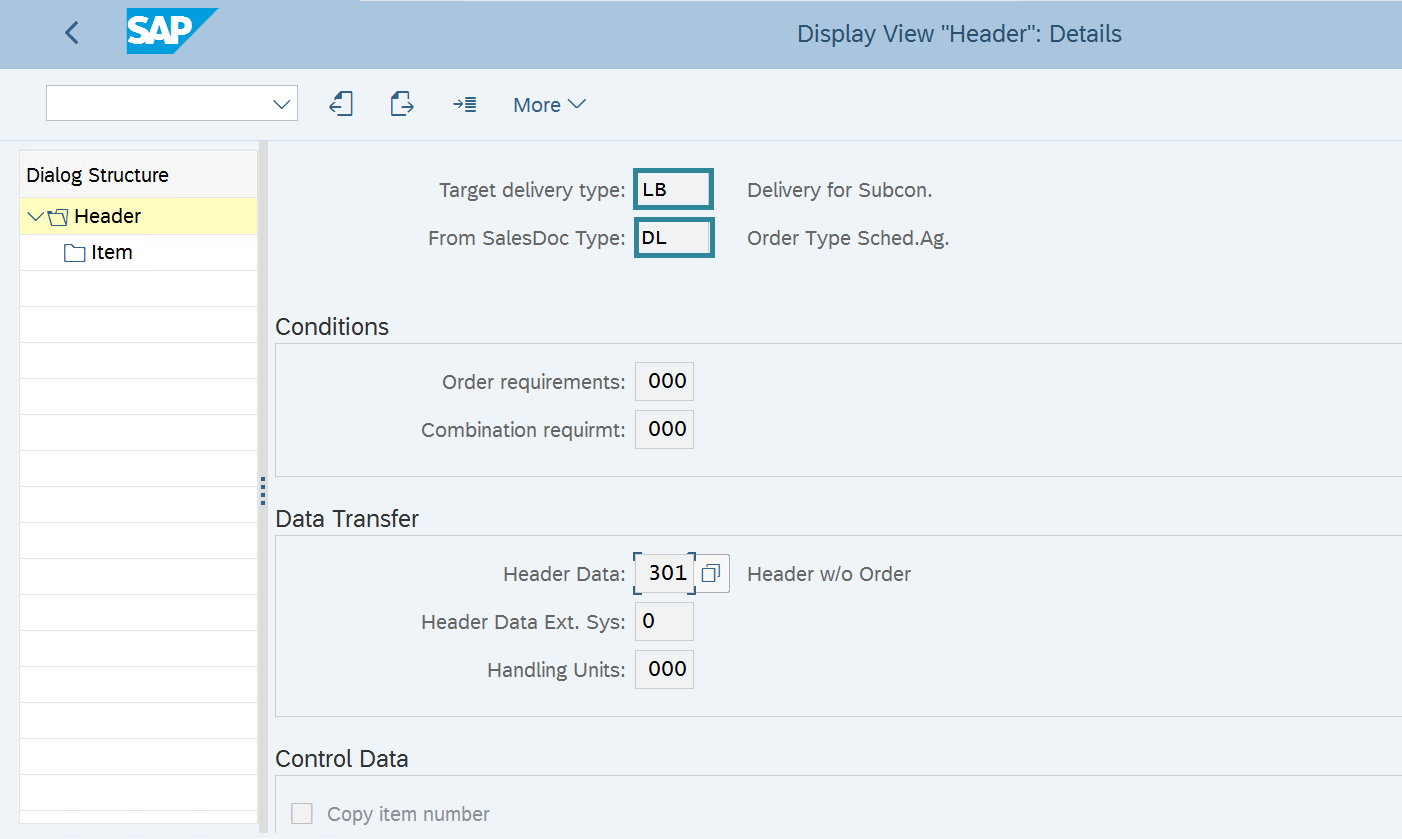
The setup should already be done for you; these are all standard configuration settings which are typically pre-delivered.
Conclusion
That’s about it. I showed how the Subcontracting process has a default delivery type per plant, how that delivery type contains a default (“dummy”) sales document type, and how those two objects are connected through the standard Order/Delivery Copy Control. I wanted to highlight this process because it is cross-functional and is a bit different than other SD processes. What do you think? Have you had to do much with your default SAP Subcontracting Delivery Setup configuration? Please let me know in the comments. Thanks for reading.
This looks really good.
While going through this, I got a doubt.
Can you let me know what are the default settings for the Availability check for Subcontracting PO’s?
Nice docs. I have a question. How to manage serialized material for subcontracting repair? We are sending and receiving same material and same serial numbers. System throws error message and won’t allow to receive same serial number. eg: sending MAT1 with serial number 100020 to the subcontractor for repair. We want to receive back MAT1-100020. (here material and components are MAT1 only)
Thanks for the question, Kumar. Without knowing the error message, it is tough to diagnose the issue. I suspect, however, that the issue is that perhaps the status of the serial number is not being updated properly. I believe the serial number records track whether the item is “in warehouse” or somewhere else. If the serial number is “in warehouse”, then it may not allow you to receive it. Does this sound familiar?
Thanks for your reply. Serial number is in warehouse only. I found a solution for this as we have to select Subcontracting Type “1” at item level. System will allow to receive same serial number after subcontracting
Hi I have a error,that message no.vl561. how to resolve?
I’m sorry, but I don’t have that error code memorized. Perhaps if you supplied some additional information like the error text, business process you’re executing, and other relevant details?
Hi Michael, Thank you for your article on subcontracting. I have several questions on this subject. I am trying to create a subcontract delivery with reference to subcontract purchase order. All the OSS notes say that can not be done.
I have tried ME2O and I have also tried VL10B to create the delivery. The later does not find any results.
In your documentation you mention “STO”. I wasn’t sure if you meant intercompany stock transfer or Purchase order. Are you suggesting that a subcontract Purchase order and delivery can be linked?
I tried the instructions that you documented. I am still not getting the desired result. I believe I have all settings as you suggested. I wanted to confirm if my understanding is correct.
Hello, Viv. Thank you so much for pointing out my faux pas! Indeed, I was typing “STO” when I intended to write “Subcontracting”. I went ahead and updated the article. Based on your comment, it appears that you are not seeing any demand for components in your ME2o report. Is this correct? Did you confirm that you have components in your Purchase Order for the subcontracting item? When you components listed (either manually, or from a BOM) in the subcontracting PO item, they should appear as demand inside of ME2o. The ME2o screen is a type of stock monitoring tool you can use to make sure you have enough components at the vendor location. The report should compare quantities on-hand at the vendor with the overall demand from Subcon PO’s. If there is a shortage, it should let you know that you is additional quantities needed. There is a button in ME2o you can click to initiate a fulfillment delivery, I believe. Let me know what you are seeing. -Michael
Good blog.
Is the item category to be used in this process in a sales order still tads?
Thanks for the comment. I scanned my article, but it looks like I didn’t include any item details. I’m not sure if it’s TADS or something else.